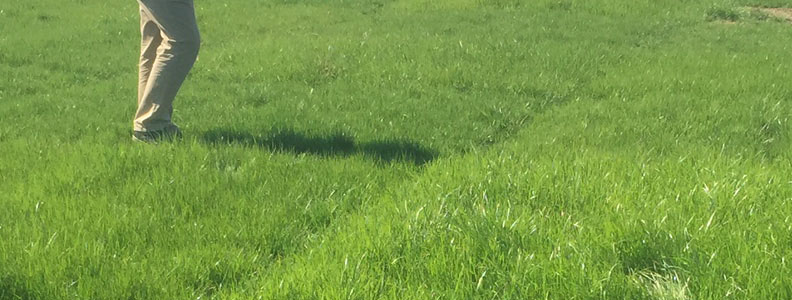
Planting the seed
Can you imagine spending ten years developing an idea, researching its viability, spending countless hours and in excess of $1 million on bringing it to fruition, only to have to scrap it at the final hurdle?
Welcome to the reality of turf grass breeding and seed production.
Having just had the pleasure of spending two days at the PGG Wrightson’s research and production facilities just out of Christchurch in New Zealand, I have had my eyes opened to the world class intellect and methods that are just across the “ditch” and within Australia.
The vision required for effective research and development into new seed varieties is remarkable. Having the ability to continually identify the needs of the industry a decade in advance is no mean feat, and when combined with brilliant powers of observation as to the attributes of plant material already in existence, researchers are continually challenging themselves and their resources in the quest for better varieties.
However, the journey has only just begun when the idea comes to mind.
It is no good if the best looking plants don’t produce seed, or at least not enough for viable production needs. This in itself can take a year or more of pain staking cross pollination to produce a teaspoon or two of seed that can then be planted out to determine if this potential new variety will in fact be a viable seed producer. If not, forget it!
Selections are planted out in the form of thousands of plugs to observe their behaviour and qualities, with the numbers then whittled down as quality control removes rogues that don’t make the grade, until finally a handful might be deemed worthy of further investigation.
Critically, any species that is considered worthy of further development must have its parental genes protected by strict quality control and storage methods, so that should there be a disaster at some point in the future, the process of producing a potential best seller can be started all over again.
This seed bank is known as the Nucleus seed and is the first of three stages, the others being the basic and breeder’s stage.
During this time, trial plots are established and maintained for a number of years, with observations recorded for long term quality control to ensure sustained performance when the variety gets to market.
By the time regulatory requirements are met in the breeding process, a decade has passed. But at any point along this process, sub-standard performance of a variety can lead to the heart breaking decision to pull it from development, a decision that can cost hundreds of thousands of dollars, but ultimately save credibility and ensure quality in the market.
Then the fun begins!
Production farming is an intriguing process. Seeding rates of 12kg/ha for rye grass and 5kg/ha for browntop bent are typical (that’s not a typo!), and have been found to provide the best plant and seed head development for harvesting. Hygiene of the paddocks is critical, and crop rotation plays an integral role in assuring purity of strains. Segregation distances are closely observed to protect from cross pollination. Protection of plant health is paramount. Careful management of growth and seed head height ensure efficiency and quality of harvesting. So important are these factors, PGG Wrightson has a team of field agronomists whose sole role is to support the farmers in the production of the best possible crop each year.
This is a strongly regulated process, with the identification of seed able to be traced back to the very paddock it was harvested from, with strict identification codes clearly displayed at each paddock and maintained throughout the production process and the life of the product.
Once cut and windrowed, the material is allowed to dry in the field for 7-10 days before being harvested to remove the worst of the debris and chaff. Getting field dressing process right is in the best interests of the farmer, as they are only paid for the viable seed that is produced, so if they freight tonnes of waste material to the machine dressing plant, it is at their cost.
Planning of machine dressing starts the moment seeding takes place in the farmers paddock, with the identification code documented and estimated harvest dates set so that the demand on the facility can be carefully managed to ensure quality is not compromised.
Once harvested seed arrives in the truck, an extraordinarily comprehensive process of quality checks begins, with testing and documentation undertaken at various stages, and cross checking undertaken to ensure that every batch of seed is at the correct stage of dressing and stored exactly where it should be. If there is any breakdown at any point in this process, production ceases and an investigation commences. If necessary, seed will be rejected.
Once bagged and stored, testing continues in line with regulatory requirements, often every six months, and then just before shipping. Again a team is dedicated exclusively to this process.
The scale and precision of the Ashburton seed dressing plant is incredible. Infrastructure worth tens of millions of dollars is all around you, with 2ha of storage sheds alone, including some refrigerated storage. The fact that this is one of seven PGG Wrightons have throughout the country is testament to the scale of this industry within New Zealand and Australia, and their reputation as world leaders in seed production.
So next time you open a bag of seed, take a look at the tag and stop to think about the work that has been done to bring that quality to your doorstep, because the attention to detail in quality control has to be seen to be believed. It is critical to our industry that we continue to respect and support companies that invest so heavily in our industry (think chemical production as well), because the reality is turf represents a very small percentage of their business, and we need to protect their interest.
If you ever have the opportunity to visit a facility such as PGG Wrighton’s, take it up in a heartbeat, because there is so much to learn about the development of the products we use and often take for granted on a daily basis.
Thanks to Guy Thomas, Mark Shaw, Grant Bunting, Bill Walmsley, Keith Salsbury, Phil Prendergast, Jason Francis and the entire PGG Wrightson team for their time. They do an amazing job, and are bloody good blokes to boot!